Kompass™
cognitive Product inspection
KOMPASS inspects at 12,000 PPM with 99.9% accuracy, while others struggle to balance speed and precision. Powered by adaptive AI and patented anomaly detection , it delivers autonomous action at scale for high-demand manufacturing.
HOW IT WORKS
How Kompass Delivers 99.9% Accurate Inspections
Kompass understands the entire product inside-out, adapting in real time to spot subtle flaws and prevent unseen anomalies from slipping through.
SEE
Kompass captures ultra-high-resolution
images from multiple angles (up to 200
images in 0.8 seconds), creating a 360° product profile for exhaustive real-time inspection.
images from multiple angles (up to 200
images in 0.8 seconds), creating a 360° product profile for exhaustive real-time inspection.
UNDERSTAND
Using high-speed parallel image processing, Kompass simultaneously analyzes defects, dimensions, print data, and inventory in a single scan - eliminating slow, sequential
ADAPT
With adaptive anomaly detection, Kompass learns from new products and defect patterns without reprogramming, adjusting thresholds to minimize false rejections.
ACT
With MES/ERP integrations, it auto-corrects deviations, and coordinates with robotic arms & conveyors to sort/reject faulty items. When defects exceed thresholds, it triggers process adjustments and records quality data.
WHY Kompass STANDS APART?
Outperforming Traditional AI-powered and Non-AI vision systems
NAGARE
Unmatched Speed & Accuracy
Advanced 360° Product Inspection
Breakthrough Anomaly Detection
Autonomous Action & Real-Time Correction
Minimal Data Requirements
NPI Ready from Day One
Turnkey Hardware Integration
Rapid Deployment
Configurable to Your Needs
KOMPASS
Inspects at 12,000 PPM with 99.9% accuracy.
Captures 200+ high-res images per product from multiple angles, leaving no blind spots.
Patented CNN + memory-based AI cuts false positives by 40–60%.
Instantly rejects and sorts faulty items, auto-corrects deviations via MES/ERP integration.
Trains on fewer than 10 good samples - no defect data needed.
Inspects new products, flags anomalies, and begins quality checks right away.
Ships with compatible industrial-grade hardware - no third-party dependencies.
Go live in as little as 6 weeks.
Lets you fine-tune inspection speed vs. quality for your production goals.
Traditional AI
Often capped at ~1,000 PPM; struggles to handle large-scale operations.
Uses limited angles, increasing the risk of overlooked defects.
Suffers from higher false positives, reducing reliability.
Relies on manual sorting and corrections, delaying defect management.
Needs 100+ good samples and labelled defect samples, slowing deployment and scaling.
Needs extensive data collection and training before inspecting new products.
Relies on external hardware, risking compatibility issues and delays.
Often takes 6+ months due to large data and training bottlenecks.
Lacks comprehensive configuration options, limiting flexibility.
IMPACT
The numbers that matter for your bottom line
99.9%
Defect Detection Accuracy
40%
Reduction in False Rejections
33%
Increased Throughput
ROI
in 8–12 Months
Key USE CASES
One platform, endless inspection applications.
Kompass adapts to any visual quality control challenge, from microscopic surface defects to complex assembly verification, all with the same powerful AI engine.
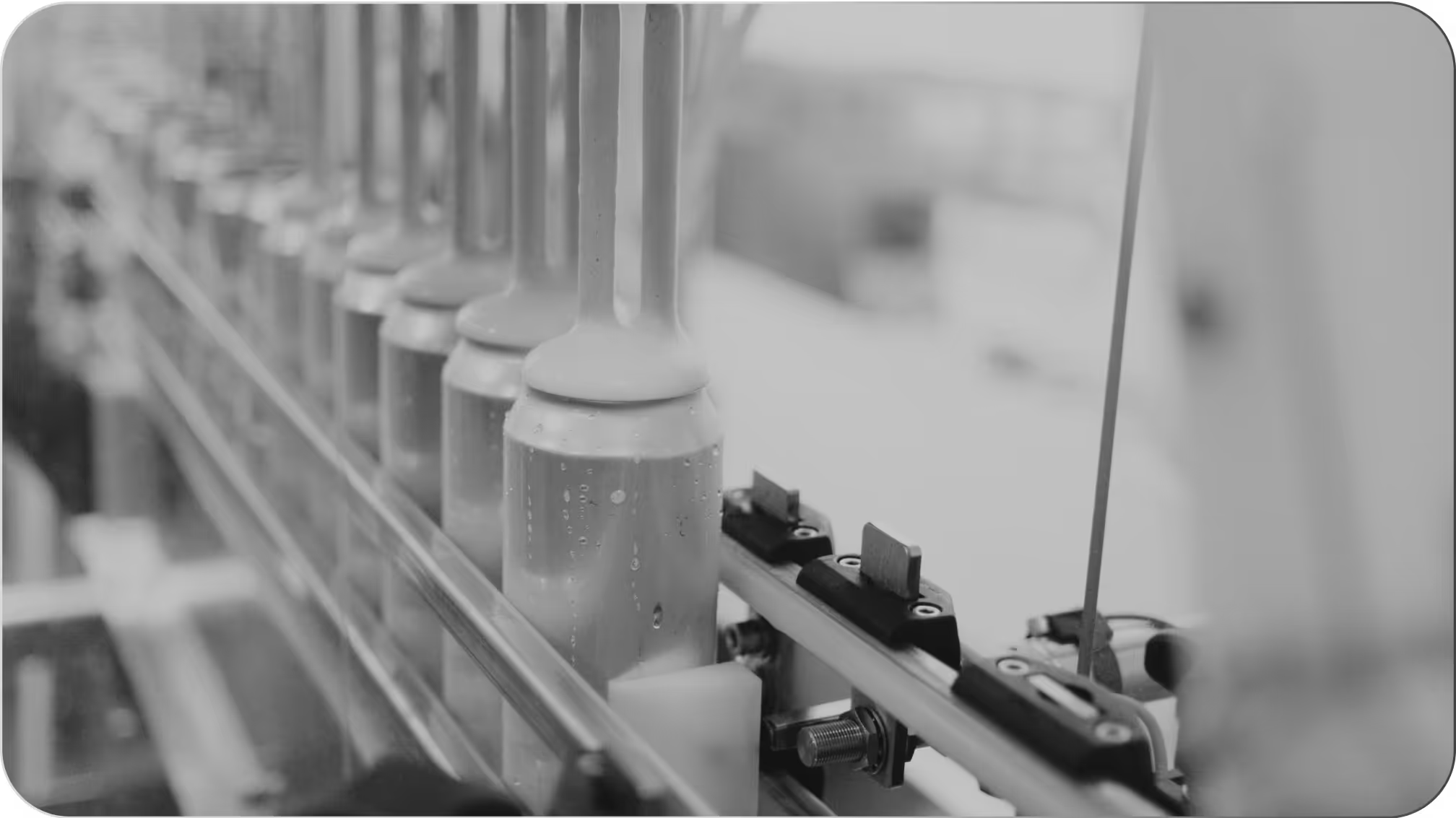
Defect Detection
Reliably flags and categorizes defects, including those not in predefined libraries - ensuring consistent quality for any product variant.
Learn More
Sorting, Counting & Classification
Automates part separation and tallying while classifying products based on defect type or production stage.
Learn More
.avif)
.avif)
Label Verification & Text Recognition
Validates text, barcodes, and graphics in real-time across packaging, labels, and direct part marking to minimize errors and returns.
Learn More
Inventory Record Accuracy (IRA)
Maintains precise, real-time counts by detecting presence or absence of components, feeding accurate data into ERP/MES systems.
Learn More
.avif)
.avif)
Multi-Component Assembly Verification
Confirm correct component presence, positioning, and orientation in complex assemblies with 100% inspection coverage.
Learn More
CONNECT WITH OUR EXPERTS
Discover how Jidoka can help you reduce costs & improve efficiency.
Get in touch